Operational Excellence
A successful transformation considers these 6 dimensions
Throughout your project, our approach is based on a constant focus on six essential dimensions. This structuring framework reinforces the coherence of your actions and sustainably supports the success of your transformation.
Vision
The systematic way in which a service is designed, implemented, and maintained to ensure an effective and consistent delivery to clients.
Excellence of processes
A structured approach to identify, anticipate, and align the needs for human capital, skills, and responsibilities with the requirements of transformation.
Skills of your resources
Analysis of the technologies and tools in place to support the processes, as well as opportunities for integrating artificial intelligence.
Continuous Improvement
Analysis of the governance mechanisms surrounding decision-making, risk management, and responsibilities, in order to ensure a transparent, coherent, and effective operation of the organisation.
Culture
Analysis and optimisation of processes, methods, and operating procedures with a view to simplifying the sequences of activities, increasing efficiency, and streamlining operational functioning.
Data & Information
Analysis of the available data and the information derived from it, in order to assess their quality, usage, and contribution to decision-making.
The key steps of a successful transformation
Credentials
In a context of rapid growth through acquisitions, a European player in the production of flexible plastic films has identified the need to enhance the efficiency of its industrial operations. Historically driven by tactical decisions, operational practices varied significantly from one site to another, thereby limiting productivity gains and the achievement of budgetary objectives.
Our client, operating more than 15 production sites in Europe, has commissioned us to intervene in a key department, with the aim of improving productivity and contributing to the consolidation of the group's EBITDA.
| Industrial diagnosis | Standardisation of practices | Optimisation of machine speed | Workplace ergonomics | Operational implementation | Change management |
- Work-related hardship, directly affecting the retention of skilled operators.
- Machine speeds largely sub-optimal, without a standard reference.
- Actual performance significantly below the set budgets.
- Heterogeneous practices among operators for similar tasks.
- Absence of predictability in production, complicating industrial management.
- Chronic difficulties in meeting the planned quantities within the allocated timeframes.
- Conducting a thorough diagnosis of the department to identify performance losses (time, energy, movements, coordination).
- Task and motion analysis according to the principles of SMED and industrial ergonomics.
- Tests and simulations of optimal speeds on the different types of machines.
- Definition of a standard production reference, recorded in the ERP and usable as a management basis.
- Construction of an "operational choreography", enabling a smooth and synchronised execution of key tasks.
- Pilot tests and deployment of new practices in a real environment, with team training.
- Targeted improvements at workstations to reduce strain and streamline operations.
+285% productivity observed in the targeted area, thanks to the standardisation of practices and the optimisation of machine parameters.
Notable improvement in work quality, reducing social tensions and the risks of absenteeism.
Documentation of performance standards in the ERP, ensuring their dissemination and sustainability.
Positioning of the site as a performance model within the group, and a focal point for subsequent deployments in other industrial units.
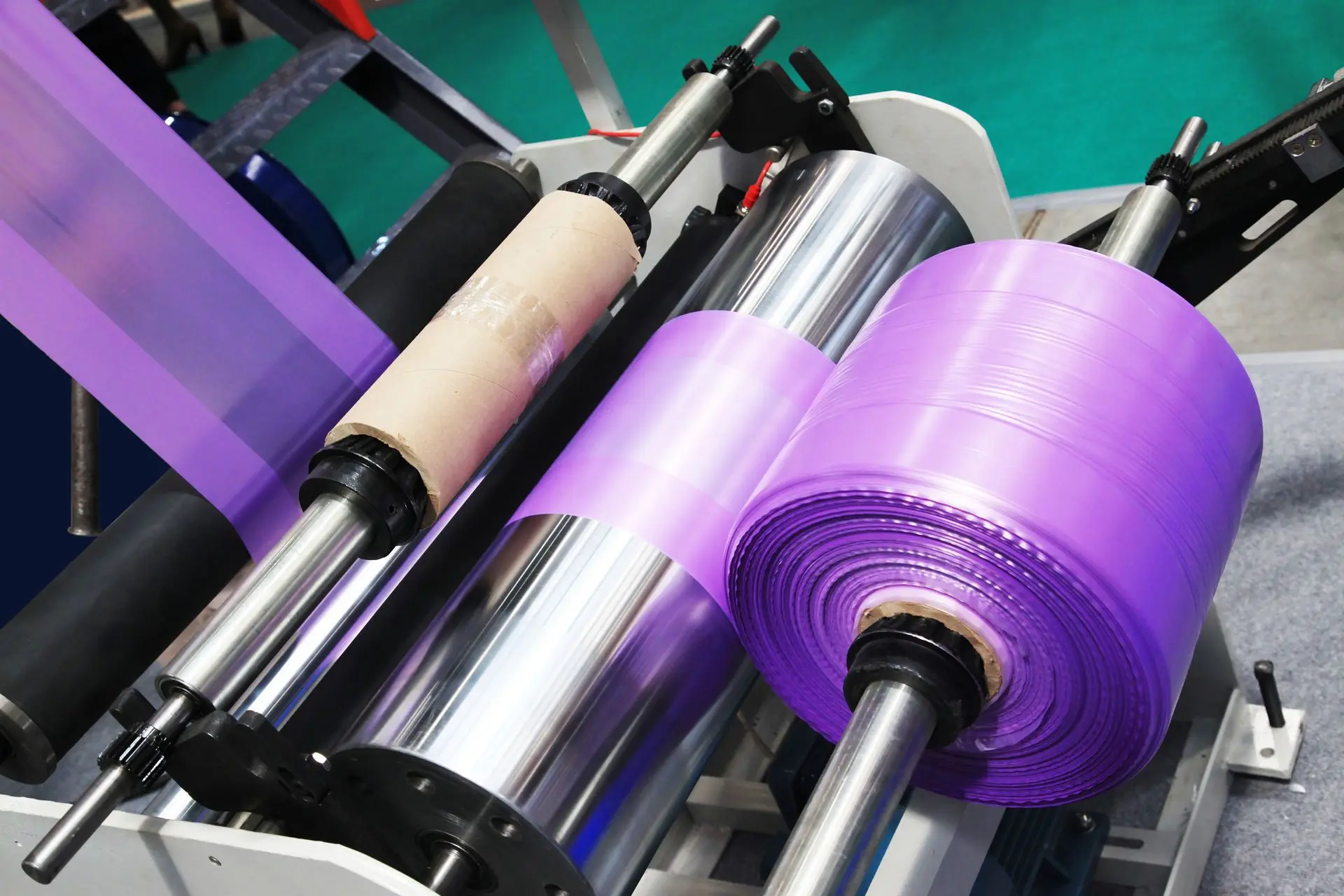
And you, are you satisfied with your operational efficiency?
You’re one click away from taking things to the next level.