Procurement & Supply Chain
The key elements of an optimised Supply Chain
The supply chain plays a central role in the smooth flow of goods and services. It encompasses the entire process, from the procurement of raw materials to the delivery to the final customer. Efficient supply chains enhance competitiveness, reduce costs, and stimulate innovation, thereby significantly contributing to economic growth and stability.
Planning
Scheduling, Capacity Planning, S&OP, and IBP are essential tools today for ensuring synchronisation between demand and capacity, optimising resource utilisation, securing operational execution, and enhancing the resilience of the Supply Chain.
Procurement & Purchasing
Strategic selection of suppliers, optimisation of purchasing, drafting of specifications, management of tenders and risk management, in order to ensure a resilient and reliable supply chain, contributing to overall operational excellence and enhanced EBITDA.
Manufacturing
Optimisation of production lines, implementation of continuous improvement initiatives, and management of industrial performance to increase availability, efficiency, and quality (OEE), enabling agile, effective production aligned with customer requirements.
Logistics & Distribution
Order fulfilment management, warehousing, internal and external logistics, distribution, last mile delivery, transport optimisation, and customer service quality — all essential levers to ensure a best-in-class OTIF (On Time In Full) performance level.
Data & Technology
Supply chain digitalisation (ERP, APS, TMS, WMS, etc.), systems integration, data quality and reliability, analytics, process automation, cybersecurity, and digital traceability.
Strategy & governance
Alignment of the supply chain with corporate strategy, management of key objectives (cost, lead time, service, sustainability), network optimisation, process governance, and performance indicators.
Optimise your operations, align your teams, enhance your profitability
Credential
This personal reference refers to a publicly listed company, specialising in the manufacture of high-tech seats for the aerospace industry, and a key supplier for all major airlines.
The "Spare Parts" unit has faced a significant increase in demand, coupled with high volatility and growing complexity in managing thousands of references (SKUs). This combination of factors has resulted in recurring delays and a notable deterioration in the on-time delivery rate (OTD).
The situation rapidly deteriorated to the point that some of the unit's most important clients blacklisted the company, jeopardising not only the reputation of the business but also its profitability and commercial prospects.
| Operating Model | Change Management | Project Management | Optimisation | Procurement | Warehousing |
This is a personal credential
- A performance breakdown in a critical segment of the activity
- An explosion in demand, poorly anticipated and poorly absorbed
- Excessive complexity in the management of references (SKU)
- Recurring delays and a drop in the on-time delivery rate (OTD)
- A failing management and a lack of medium-term visibility
- A siloed organisation and a lack of alignment between key functions
- A fragmented and inefficient logistics system
- A lack of operational autonomy in the "Spare Parts" unit
- Deployment of a master planning process (MPS) within the production workshops, accompanied by the development of a customised tool and the formalisation of user documentation, ensuring its sustainability and accountability by the teams.
- In-depth analysis of logistics performance, including lead times, on-time delivery rate (OTD), demand patterns, safety stock parameters, and reference segmentation through ABC analysis, in order to enhance the responsiveness and accuracy of operational decisions.
- Implementation of decision support tools for purchasing, incorporating simulation functions, in order to guide actions according to suppliers and critical product families — objective: reduction of lead times and targeted improvement of OTD.
- Reorganisation of physical flows in the workshop, including a rearrangement of the layout and material circuits to increase productivity and limit non-productive time losses.
- Complete transformation of logistics processes, from receiving to shipping (including quality control and packaging), with the creation of a unified, streamlined, and optimised flow to maximise warehouse efficiency.
- Strengthening the coordination between customer service and the supply chain, to improve perceived service quality, reduce friction, and align operational priorities with the expectations of key customers.
- Strategic separation of the flows of spare parts and main production, in order to reduce interference, streamline operations, and improve the specific performance of the "Spare Parts" unit.
A structured capacity planning system has been established, allowing for the projection of workload and capacity in the medium term. Decisions are better anticipated, and trade-offs are facilitated.
The on-time delivery rate (OTD) has been significantly improved: the defined objectives are consistently met, restoring reliability with respect to strategic customers.
Visual management tools have been deployed, enhancing the teams' ability to manage in real time, detect discrepancies, and proactively adjust action plans.
The autonomy of the "Spare Parts" unit has been significantly strengthened, thanks to the clarification of flows, responsibilities, and processes, allowing for more effective management of orders and better control of deadlines.
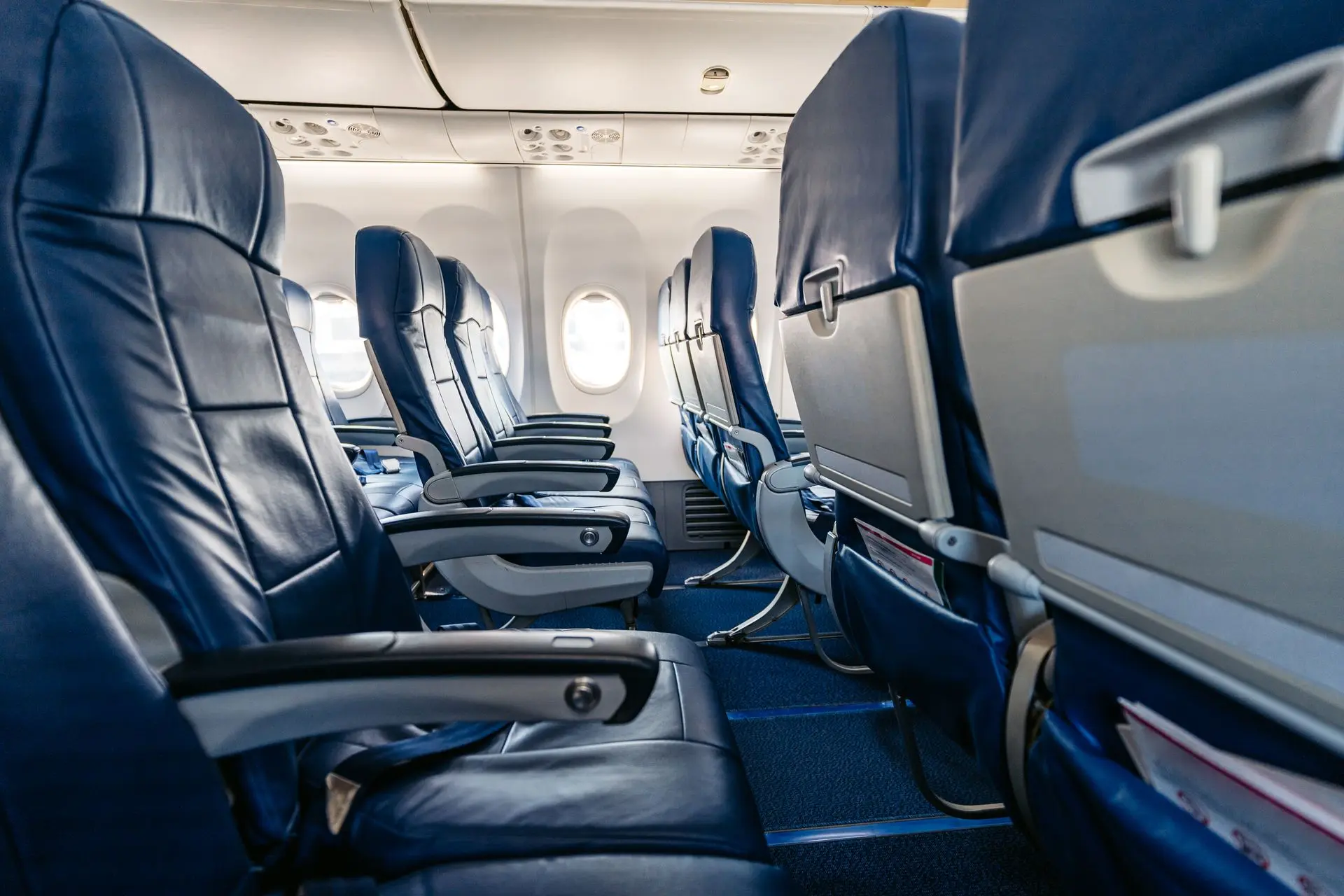
And you, is your supply chain optimised and has it become a competitive advantage?
You are one click away from taking it to the next level.